APS to the Rescue! How We Helped Complete a Pipeline on Time
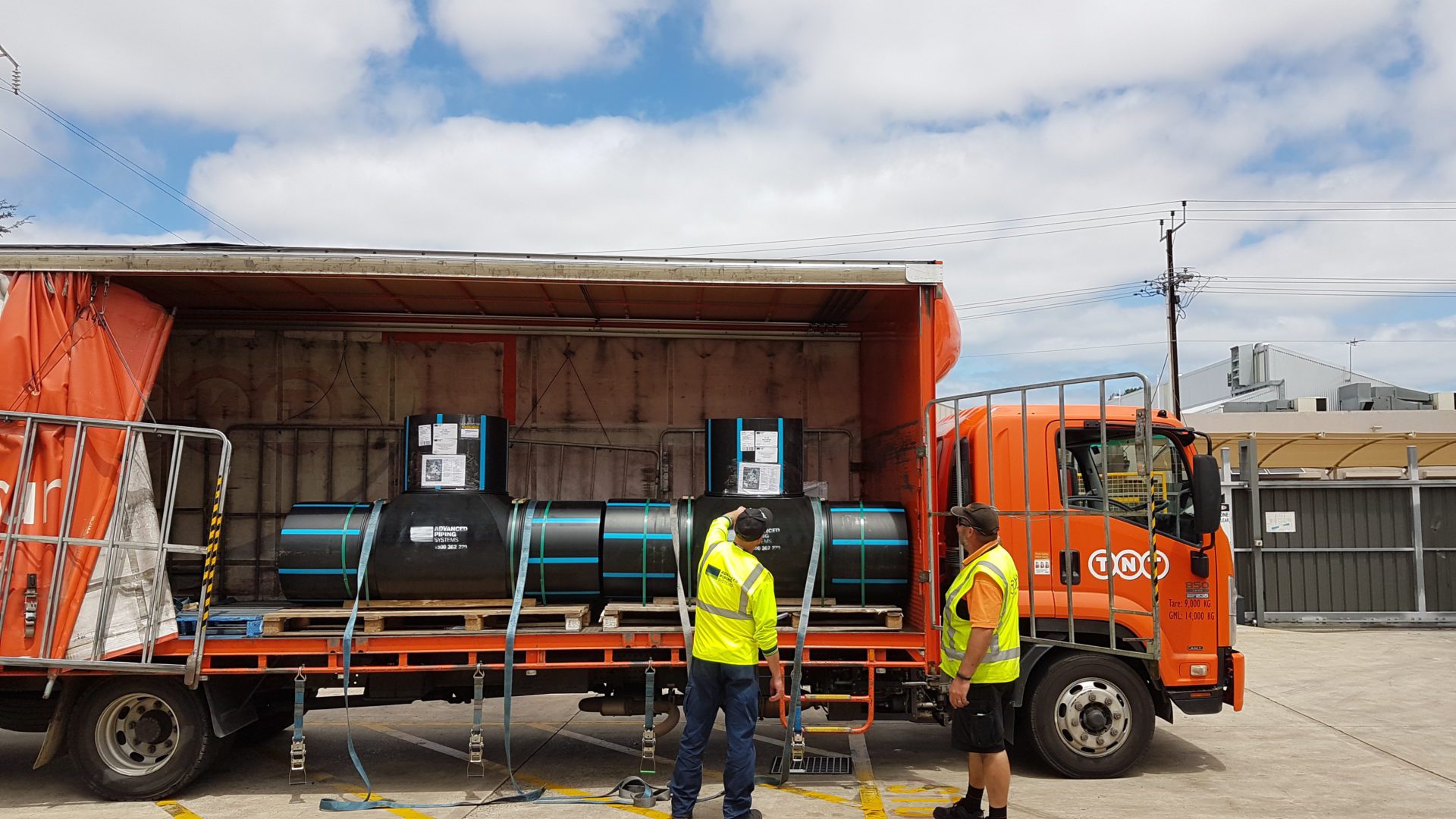
When a new HDPE pipeline was being built to supply treated water to a coal mine and power station in New South Wales, time was ticking. Their supplier of HDPE pipe and fittings wasn’t coming through.
This article tells the story of how Advanced Piping Systems was able to help the project team deliver on time.
Major HDPE pipeline project facing massive delays
Pipelines for coal mines and power stations transport highly corrosive water. On the one hand, pure water is an input power station; and coal-silk-rich water is an output. Both are highly corrosive.
This meant that only polyethylene pipe was suitable for the project. The entire pipeline was specified in polyethylene pipe.
The constructing company, a specialist in complex infrastructure, was highly experienced in completing large and complex pipelines for water, water treatment, sewers, and energy. Regardless, their project was still experiencing major delays. It almost seemed that they were not going to be able to get the pipe and fittings that they needed.
In a situation like this, extended delays can impact on their reputation as a subcontracting company.
It’s not for us to guess at why the supplier couldn’t meet the requirements of the project in the time demanded. However, we do know that some major suppliers will agree to orders without problem-solving the project from end-to-end. The sheer size of the project would have caused trouble for any single supplier.
A combination of good timing meant that one of our sales team was in the same region of New South Wales as the pipeline’s project team. Making a courtesy call to them to see if there was anything he could help them with, he learned about the problems the team was facing.
This sparked a meeting and a conversation. And for the next four hours, he sat in their offices completing quotes and orders. Before he left, the first shipment from our location in Adelaide was already on its way.
The pipeline had some very specific requirements, that no major supplier would have easily been able to complete. The reason that we could meet their requirements is because of our lean fabrication processes. They are not only fast, but bespoke.
As a result of our ability to keep delivering exactly what the project team required, at speed, we ended up supplying two or three orders per day for that project until completion.
Your key takeaway
Large pipeline projects—we estimate that this project may have run to approximately $5 million in total for the company we supplied—it’s vital that you have a supplier who will do the planning to make it work.
While we pride ourselves on delivering outstanding service like this, even at very short notice, the reality is that if we couldn’t do it, we wouldn’t have agreed to the job. And we would only know that if we spent the time up-front to do the planning.
That’s partly how we were able to keep delivering for this project, from the very first order. Having spent time on site to understand their requirements, and work on a plan, we knew that we could get them moving again.
If your supplier isn’t able to tell you how they plan to deliver on your work, make sure you have options just in case. As someone managing a large and potentially unwieldy project, you know yourself that it’s better to have options than to be embarrassed that your project isn’t hitting its targets.
Managing a HDPE pipeline project like this requires the right handling , before you hit crisis point
With the right suppliers and information, you will be able to make good decisions, confident that you’re working with professionals who have your best interests in mind. To stay informed with the latest information that will keep your pipeline moving, opt into our mailing list today.