Why Your Pipeline’s 90-Degree Elbow Is at Risk and Could Cause Downtime
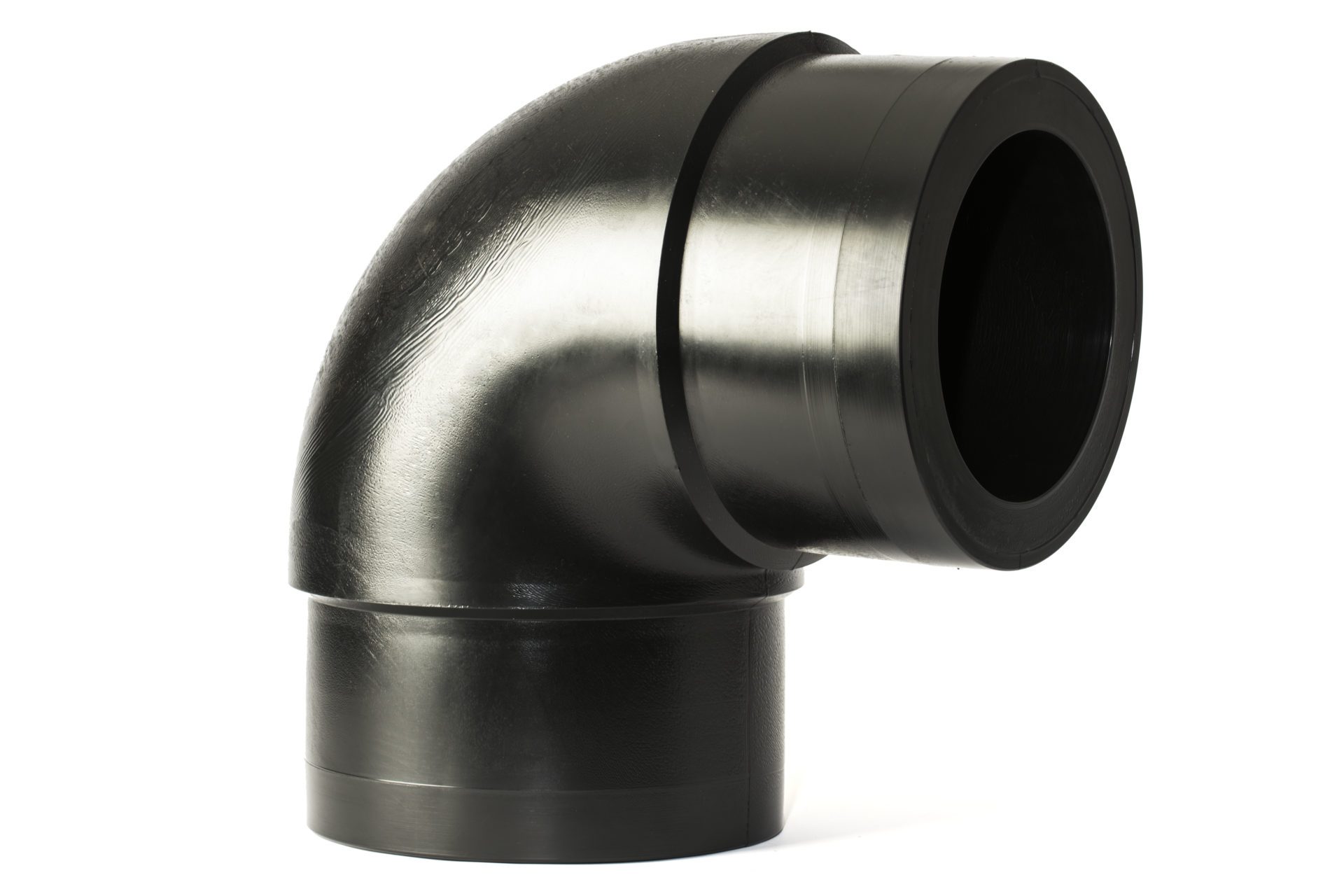
Here is why 90-degree elbows, spigot elbows, are putting the performance of your pipeline at risk: they create friction loss, slowing everything down. And turbulence that will wear out your line much faster.
Why your long spigot elbows are a maintenance risk
The type of spigot I am referring to is the long spigot elbow: A 90-degree bend that doesn’t have any radius. They form a hard-internal corner. From the perspective of putting in a necessary turn, they appear to be efficient.
To illustrate why this is problematic, I want you to think about flying down a road in your car at 110 kph. A sharp corner comes up. You attempt to go through the corner, but at that speed if you don’t roll your car, you will certainly wear your tyres out.
A similar principle applies to pipelines. A hard, 90-degree corner results in a huge amount of force (or steam) hitting the corner.
This then does four things:
- It slows down at the bend
- It creates a catch-point, which can become a blockage
- It restricts the flow-rate, making your pipeline less efficient.
- You get sedimentary build up leading to point 2 above.
Your primary concern when maintaining a line is probably not going to be the flow-rate. You are most concerned about getting the line up and moving again, as cheaply as possible.
Comparing prices is like comparing apples with oranges
If you’re thinking about cost, a long spigot bend might well be the cheapest option. The issue is that it’s only cheap initially.
Over the long term, what you save in cost now will be irrelevant when you have to keep replacing the corner. It doesn’t matter what type of pipe materials you’re using; a hard 90-degree bend is going to wear out, creating a continuous maintenance issue.
All bends are not equal, and sometimes the option that looks like the best one simply creates more problems.
So what’s the alternative?
The alternative is to put in a 1D or 1.5D sweep bend: It’s a radius bend with a longer bend radius. This is going to give you a much longer life-span in a high-wear situation, and will reduce your maintenance requirements, significantly increase flow and reduce pressure drop.
At Advanced Piping Systems, we will always make sure that the bends you request from us are going to be the most valuable for you. While we won’t specify bends for you, we have decades of experience supplying materials and components for pipelines in all kinds of situations. To double-check whether what you think you need is actually what’s going to work for you, pick up the phone and give us a call on 1300 789 178.
Keep your pipeline moving at speed, with minimal maintenance
Get the right information to keep your pipeline moving, while keeping your maintenance efforts at a minimum, opt into our mailing list today.