Debottlenecking Episode 2
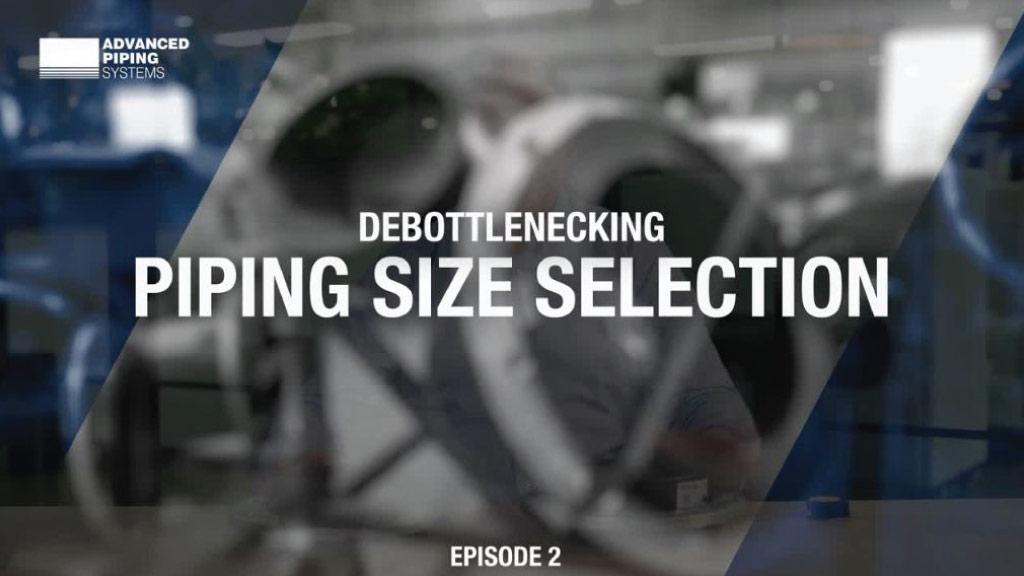
Role of inside diameter (ID) in piping systems
Debottlenecking Episode 2 is now available! When making a pipe or fitting selection with performance in mind, deciding on the role of Inside Diameter (ID) in piping systems is a crucial part of the decision-making process. ID refers to the inner diameter of the pipe or fitting, which determines the flow capacity or volume inside the pipe. We offer two standard flange sizes in each pipe class with a different ID, providing the ultimate flexibility and choice.
We recently worked on a project that originally requested 200 mm SDR17 piping. Our team reviewed the project and identified that using a 225mm SDR11 pipe rather than the 200mm SDR17 they requested would add much-needed longevity to the pipes. While both have matching 8” 200mm flange sizes, the 225mm sdr11 has a wall thickness of 20.45mm and an ID of 182.9 mm, a 57.5% increase compared to the 200mm sdr17, which has a wall thickness of 11.76mm and an ID of 175.8 mm. This small change of increasing the ID has a big impact on increasing flow, increasing production, and reducing maintenance costs. In a constant wear application calculation of 4mm of wear per year, this change could extend the pipe’s life from 35 to 61 months.
Added strength
When you enlarge pipes, you’re not just improving one section. You’re setting off a ripple effect of efficiency throughout the entire system. Selecting the correct size pipe with the right Standard Dimension Ratio (SDR) in the planning stages of your project can make a huge difference in avoiding bottlenecks in the future. SDR standardises pressure ratings for pipes of the same size but made from different materials. It is calculated by measuring the Outside Diameter (OD) and dividing it by the Maximum Wall Thickness.
We can offer an alternative in many sizes by upsizing the pipe size and SDR while maintaining a similar inside diameter and the original flange size.
In a recent example, a client contacted us to order a 150mm or 6-inch pipe – commonly known as 160mm in HDPE – which is one of the most common sizes globally. However, we identified that increasing the size to 180mm instead of 160mm, which also fits the same 6” size flange, would create a more consistent system. The 180mm pipe will provide a 13% increase in the nominal bore without needing to change associated valves and connecting equipment. This will make a particularly big difference in a gravity or pressure feed. The 180mm SDR17 has a 158mm ID friction loss, which equates to 11.13 metres head loss. This is almost half of the 160mm SDR 17, with 140mm ID and friction loss of 19.75 metres head loss.
This is a huge difference! Upsizing provided increased flow, increased pressure, eliminating blockages, decreasing pump load and power consumption, and decreasing wear.
A mismatch between your pipe and the other fittings could lead to a difference in wall thicknesses. This creates additional turbulence that accelerates wear and may mean that your system blocks due to sediment build up. By selecting a pipe which has the same ID, but a larger OD, you can create a more resilient solution. It is for this reason we recommend working with SDR17 and SDR11, as fittings are easily available in these sizes. Whereas odd SDR such as SDR21 and SDR13.6 may be slightly lower in costs and won’t match as easily, potentially causing you more in maintenance costs later on.
In the video below, Nathan discusses the differences between the 160mm and 180mm pipes. He highlights that the 160mm is the most commonly installed but the 180mm features a 13% increase in internal diameter.
We hope you enjoyed the second episode of Debottlenecking. If you would like to use the Friction Loss Calculator mentioned in the video, it’s available on the Advanced Piping website. Next week, we’ll explore Customized Solutions with Caleb, so stay tuned!