Desalination Solutions: Why HDPE is the Smart Choice
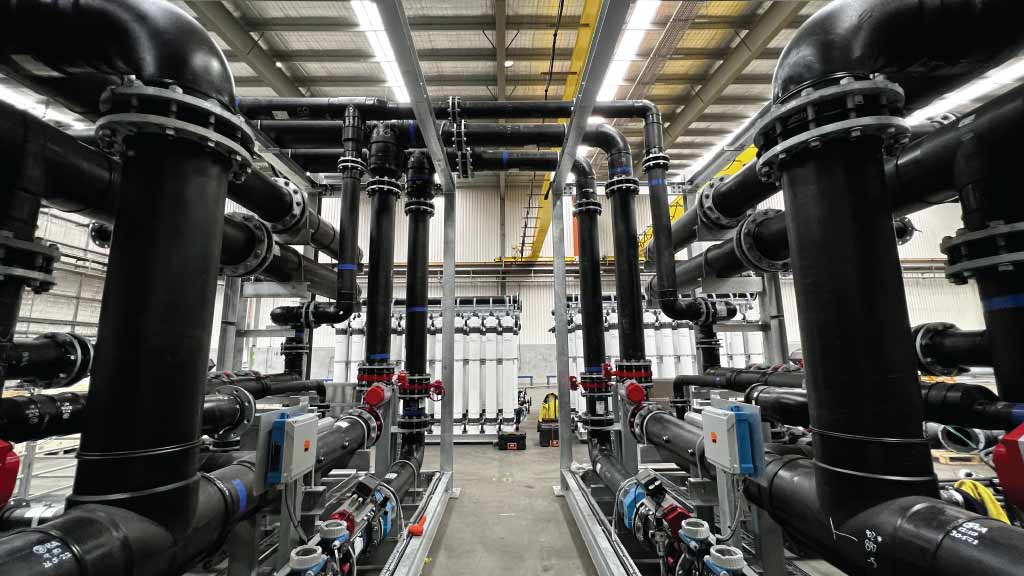
The Importance of Desalination Solutions and HDPE
As the demand for fresh water continues to rise, desalination solutions have become essential for converting seawater into potable water. When selecting materials for desalination plants, high-density polyethylene (HDPE) is the preferred choice due to its durability, chemical resistance, and ease of installation. Compared to glass-reinforced plastic (GRP), HDPE offers superior performance in desalination applications, making it the go-to material for water treatment facilities worldwide.
Why HDPE is Ideal for Desalination Solutions
1. HDPE and Seawater Compatibility
Desalination plants primarily process seawater, which has high salinity and corrosive elements. HDPE is inherently resistant to saltwater corrosion and chemical degradation, making it an ideal material for desalination pipelines and infrastructure. Unlike GRP, which may degrade over time due to salt exposure, HDPE maintains its integrity, ensuring long-term performance.
2. Superior Chemical Resistance in Desalination Processes
Chemical treatment is a critical part of desalination. It involves pre-treatment, membrane cleaning, and disinfection. HDPE’s exceptional chemical resistance allows it to withstand exposure to harsh chemicals without deteriorating. GRP, on the other hand, may not provide the same level of resistance, potentially leading to performance issues and material degradation.
3. Durability and Longevity in Continuous Operation
Desalination plants operate continuously, 24 hours a day, seven days a week. This demands materials capable of withstanding extreme conditions, such as high internal pressures and constant exposure to seawater. HDPE is an ideal material for these challenging environments due to its exceptional toughness, flexibility, and impressive resistance to cracking. These qualities make it a highly reliable choice for long-term applications in desalination plants, where performance and durability are critical. Unlike GRP, which can become brittle and prone to failure over time, HDPE maintains its strength and flexibility, ensuring that desalination infrastructure remains functional and efficient for extended periods. This enhanced durability significantly contributes to extending the overall lifespan of desalination systems, reducing maintenance costs and improving operational reliability.
4. Ease of Installation and Low Maintenance
One of HDPE’s most significant advantages is its ease of installation. It is lightweight, flexible, and can be joined through various methods, such as butt fusionand electrofusion, allowing for seamless connections. These features significantly reduce installation time and labor costs compared to GRP, which requires more complex joining techniques and additional structural support.
Explore Advanced Piping Systems’ entire range of HDPE fittings
5. HDPE is 100% Recyclable and Environmentally Safe
Sustainability is an essential consideration in modern desalination solutions. HDPE is non-toxic, recyclable, and does not leach harmful substances into the environment. It requires no protective coatings or linings, unlike GRP, which may involve hazardous materials. This makes HDPE an eco-friendly choice for water treatment applications. Read more about Advanced Piping Systems’ sustainable HDPE solutions.
6. Minimal Toxicity in Production
HDPE is primarily derived from petroleum through a low-toxicity polymerization process that produces a durable and chemically stable material. This method ensures that HDPE remains free from harmful byproducts, making it a safer and more sustainable choice for industrial applications. In contrast, GRP involves glass fibers combined with polyester or epoxy resins, which may release volatile organic compounds (VOCs) and hazardous air pollutants (HAPs) during manufacturing. These emissions can pose environmental and health risks, requiring additional safety measures in production. Choosing HDPE minimises these risks and supports cleaner and more sustainable desalination practices.
So why is HDPE the Leader of Desalination?
HDPE stands out as the optimal choice. This is due to its unique resistance to seawater and chemicals, ease of installation, durability, and environmental benefits. Its ability to withstand harsh environments and chemicals makes HDPE a reliable option for piping in desalination projects/plants. Companies in the water treatment sector choose HDPE to ensure cost-effective, long-lasting, and reliable desalination solutions.
For more information on HDPE piping solutions for desalination, visit Advanced Piping Systems, or talk to one of our friendly customer support team members. You can reach them via the online chat, the Advanced Piping contact page or by calling them at 1300 362 229.