Is Your Piping System Up to the Test?
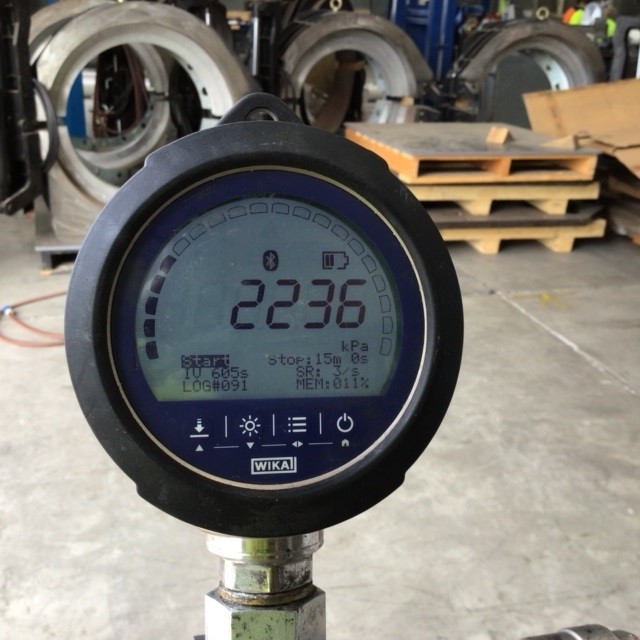
With so much riding on the performance of your piping system, the last thing you need is for something to go wrong, resulting in costly delays and repairs.
That’s why testing your piping system, whether polyethylene (PE) or steel, is so important.
Not only will testing pick up any faults or leaks in the piping, it will also give you the peace of mind that the system is going to operate as it’s intended to.
But when it comes to testing, many don’t realise that it’s not a case of ‘one size fits all’.
Steel and PE piping systems have their specific testing requirements to ensure they’re working as they need to be.
Steel and PE testing – what’s the difference?
While testing of steel and PE systems use the same general approach, called hydrostatic pressure testing, the characteristics of each product means it isn’t possible to apply a blanket method across both.
Project Manager at Advanced Piping Systems, Josh Fox, said the main difference between the two materials is that PE piping will expand and relax due to being made of elastic plastic, whereas steel piping won’t.
“Hydrostatic pressure testing involves filling a pipeline with water, bleeding the air out, pumping it up to the desired pressure, and holding it at that pressure for the test duration,” he said.
“Due to being a more flexible material, the expand, relax and settle procedure takes a considerable amount of time for PE systems, meaning completing testing will take longer than steel.
“A typical testing procedure for PE piping would see us pump the system to higher pressure than required. We let the system expand and relax like this 3-4 times, and each time the pressure loss lessens. Once the pressure settles, we then conduct the main test.
“On big bore systems we may have to leave it overnight to settle. When you are doing this for multiple tests the time can really add up.
“It’s a similar process for steel systems, however, steel doesn’t expand and relax. This means you can fill it with water, bleed the air and then pump it straight up to desired test pressure immediately.”
Testing needs are specific
Just as the testing methods for steel and PE piping differ, so too do the testing requirements of each customer.
Josh said that many customers will have their own specific testing standards or regulations that they want to adhere to.
“The industry standard is AS/NZS 4130:Polyethylene pipes (PE) for pressure applications, and at Advanced Piping Systems, we will predominantly test to 1.25 times the operating pressure of the pipeline,” he said.
“For example, if a system has a pressure rating of PN16, we will test it to PN20.
“Having said that, every customer is different and has different requirements.
“For example, a customer may want two gauges, one on each end of the system, and conduct a test for 60 minutes with data graphing.
“Another company might only need a 15 minute test at 50% pressure to ensure there are no leaks.”
Josh said it was important for each customer to give some consideration to their specific requirements prior to testing, such as the pressure and duration of the test, and whether they want graphing, certification or other documentation.
Another key consideration for customers is whether they want their piping system tested on-site, or at their supplier’s premises (e.g. Advanced Piping Systems’ warehouse).
“While you can certainly do both, there are some significant benefits to testing at our premises,” Josh said.
“In the controlled environment of our test facility, it is generally much quicker and easier to conduct the testing because there are no weather impacts to contend with and we have all resources for testing readily available, such as water which we recycle, and electricity.
“It also eliminates the significant risks associated with testing in the field.”
Commitment to quality
According to Josh, testing and certification are key components of quality assurance (QA).
And with a purpose built online QA program, Advanced Piping Systems APS can help you with all of your QA needs faster and with more detail than ever before.
“The online nature of the system means we can quickly and easily upload and access data, ensuring smoother communication with our customers and faster documentation,” Josh said.
“The entire system leads to better communication and more satisfied customers.
“QA documents are ready and sent to customers on the day of the final dispatch. There’s no waiting weeks or months for them.
“All data is entered straight into the system, including weld records, complete and sign-off on fabrication quality checks and update hydro testing forms, with the ability to upload photos before, during and after. This immediacy is great for customers and our staff.
“Documents can be sent as a package in a single PDF document, and they are easy to read.
“Historical data is also always available, so customers can always refer to previous jobs.”
Put Advanced Piping Systems to the test
We’ve got the skills, space and technology to ensure your piping system — whether PE or steel — is working as it should be.
To arrange one of our experts to test your piping system, contact our customer service team today.