Reliability-Centred Maintenance – A Tasty Little Introduction That Will Definitely Get You Hooked On
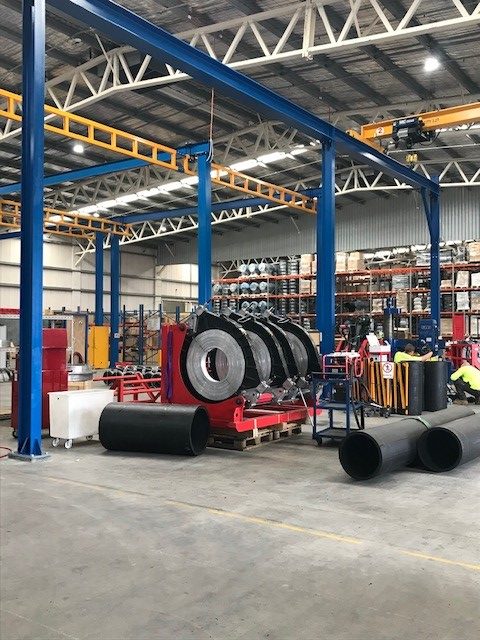
Reliability-centred maintenance (RCM) is a solid conceptual framework for maintenance management. For a start-to-finish rundown, there’s a technical SAE standard and even entire books about RCM.
This three-part blog series gives you some smart tips to boost the way RCM works for you:
- Part One introduces RCM with some terms to learn and a look at how it fits into your organisation.
- Part Two focuses on quantifying and avoiding failure.
- Part Three is about running RCM in your company: Understanding the risks you face, the documentation side of RCM, and learning as you go.
What do the RCM terms actually mean?
Reliability-centred maintenance has some specific terminology to get straight before we begin.
Firstly, the things that you and your team maintain are “assets”, and your assets fit together into a “system”. The system is what delivers the value that your company offers customers, workers, and others. That value and that network of people are the system’s “context”. Finally, when an asset (or system) stops doing its bit to deliver that value, we have a “failure”.
How are assets, systems, context and failure related?
Maintenance is about avoiding failure. Under RCM, failure is a relative concept. A system that fails in one context could succeed, unchanged, in another. An asset that’s a failing part of one system could work well in a different system. As you work on assets, the system and the context will direct your efforts.
In some cases, you might even adjust the system to shift failure away from an asset. In rarer cases you (and other leaders) might even tinker with the context to redefine—and avoid—failure.
For some managers, failure is simply another process to be managed. This is handy because it replaces the view that you’re managing a set of assets that need to keep working well.
Look at the big picture to see your context
So now’s a good time to think about context. Reliability-centred maintenance starts with big questions like, what is your organisation producing? Who for? How does your system of production work? What things are your organisation sensitive to?
Here’s a good tip: You see the context you’re in when you know what issues or system changes would lead to a business reaction.
You can’t answer big questions like these on your own. A lot of RCM is about collaborating with other managers and teams to find your system’s place in their work lives.
What do people really want from their assets?
There are people who work with each asset—its users. What do they need it to do? There’ll be more to this than “we need it to work”. What about safety? Or the way they operate it? Or the places where this asset relates to others?
Each asset’s owners will have a different set of needs. They can include regulatory compliance, economic performance, and others.
Some assets also deliver value to a wider set of people. If you’re managing environmental risk, for example, your local or national community will need the asset to function well.
What do your assets really do?
This goes beyond your maintenance team, and gives you another opportunity to work widely with colleagues. The sorts of questions you need to answer are: Why do we have this asset? What’s it worth to us? How could its failure prevent us from achieving our goals?
Collaborate, collaborate, collaborate!
As you learn about your assets’ value to the organisation, you will start to see things from new points of view. Earn support and cooperation by showing others how effective maintenance is good for them.
When your maintenance plan gets buy-in from around the organisation, it’s a big help. Achieving it will be easier when you understand what failure means to everyone you’re working with.
See you next time for tips 7-12
The RCM series will continue soon, with a look at asset failure and the value of avoiding it. To know when Part Two is out, join our mailing list today:
This three-part blog series gives you some smart tips to boost the way RCM works for you:
- Part One introduces RCM with some terms to learn and a look at how it fits into your organisation.
- Part Two focuses on quantifying and avoiding failure.
- Part Three is about running RCM in your company: Understanding the risks you face, the documentation side of RCM, and learning as you go.
What do the RCM terms actually mean?
Reliability-centred maintenance has some specific terminology to get straight before we begin.
Firstly, the things that you and your team maintain are “assets”, and your assets fit together into a “system”. The system is what delivers the value that your company offers customers, workers, and others. That value and that network of people are the system’s “context”. Finally, when an asset (or system) stops doing its bit to deliver that value, we have a “failure”.
How are assets, systems, context and failure related?
Maintenance is about avoiding failure. Under RCM, failure is a relative concept. A system that fails in one context could succeed, unchanged, in another. An asset that’s a failing part of one system could work well in a different system. As you work on assets, the system and the context will direct your efforts.
In some cases, you might even adjust the system to shift failure away from an asset. In rarer cases you (and other leaders) might even tinker with the context to redefine—and avoid—failure.
For some managers, failure is simply another process to be managed. This is handy because it replaces the view that you’re managing a set of assets that need to keep working well.
Look at the big picture to see your context
So now’s a good time to think about context. Reliability-centred maintenance starts with big questions like, what is your organisation producing? Who for? How does your system of production work? What things are your organisation sensitive to?
Here’s a good tip: You see the context you’re in when you know what issues or system changes would lead to a business reaction.
You can’t answer big questions like these on your own. A lot of RCM is about collaborating with other managers and teams to find your system’s place in their work lives.
What do people really want from their assets?
There are people who work with each asset—its users. What do they need it to do? There’ll be more to this than “we need it to work”. What about safety? Or the way they operate it? Or the places where this asset relates to others?
Each asset’s owners will have a different set of needs. They can include regulatory compliance, economic performance, and others.
Some assets also deliver value to a wider set of people. If you’re managing environmental risk, for example, your local or national community will need the asset to function well.
What do your assets really do?
This goes beyond your maintenance team, and gives you another opportunity to work widely with colleagues. The sorts of questions you need to answer are: Why do we have this asset? What’s it worth to us? How could its failure prevent us from achieving our goals?
Collaborate, collaborate, collaborate!
As you learn about your assets’ value to the organisation, you will start to see things from new points of view. Earn support and cooperation by showing others how effective maintenance is good for them.
When your maintenance plan gets buy-in from around the organisation, it’s a big help. Achieving it will be easier when you understand what failure means to everyone you’re working with.
See you next time for tips 7-12
The RCM series will continue soon, with a look at asset failure and the value of avoiding it. To know when Part Two is out, join our mailing list today: